Redefining manufacturing execution systems with Mill Pulse®
Mill Pulse®
Why choose
Mill Pulse®?
User Friendly
Designed to simplify operations
Goals Oriented
Encourage your personnel to achieve their goals
Mobile
Responsive web interface runs on all mobile devices
Integrated
Vertically integrated with your process and ERP
Flexible
Adapted to your process
Customizable
Customizable dashboards and KPIs
Get back on the race track with
Mill Pulse®
How much time do you lose in unexpected stops and product changes? Every second counts. Like a Formula 1 driver in the pit stop, a steel mill needs to minimize the time the mill is not producing. Planning, coordination, rapid response, technology, digitalization and most importantly a great team are the ways to acquire a competitive advantage. Mill Pulse® can help you gain critical time, by optimizing the mill setup, minimizing delays and coordinating teams. Designed exclusively for steel mills, the Roll Shop and Mill Setup modules included in the Mill Pulse® Suite are digitalized tools that optimize Rolling Mill pitstops, for example during a product change.
Production management and Scheduling
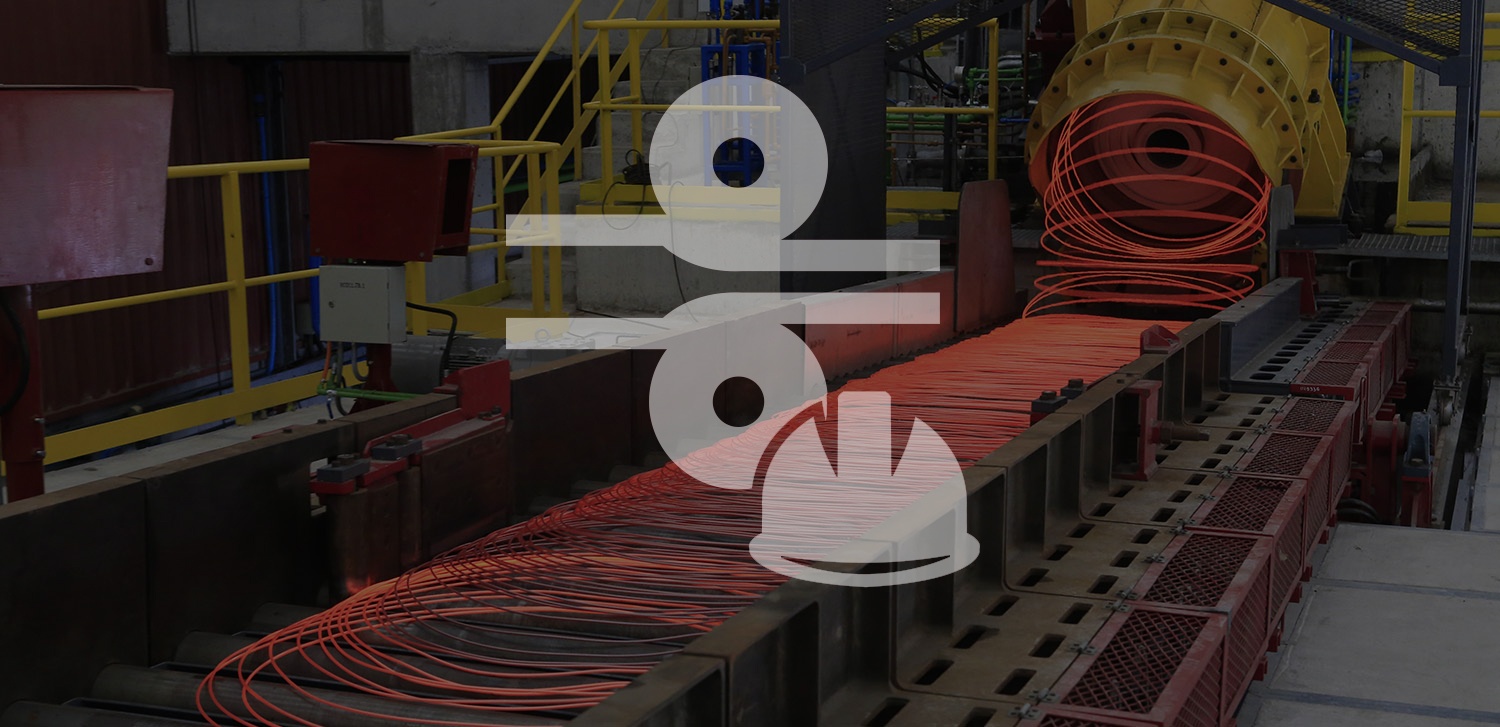
Delays Tracking
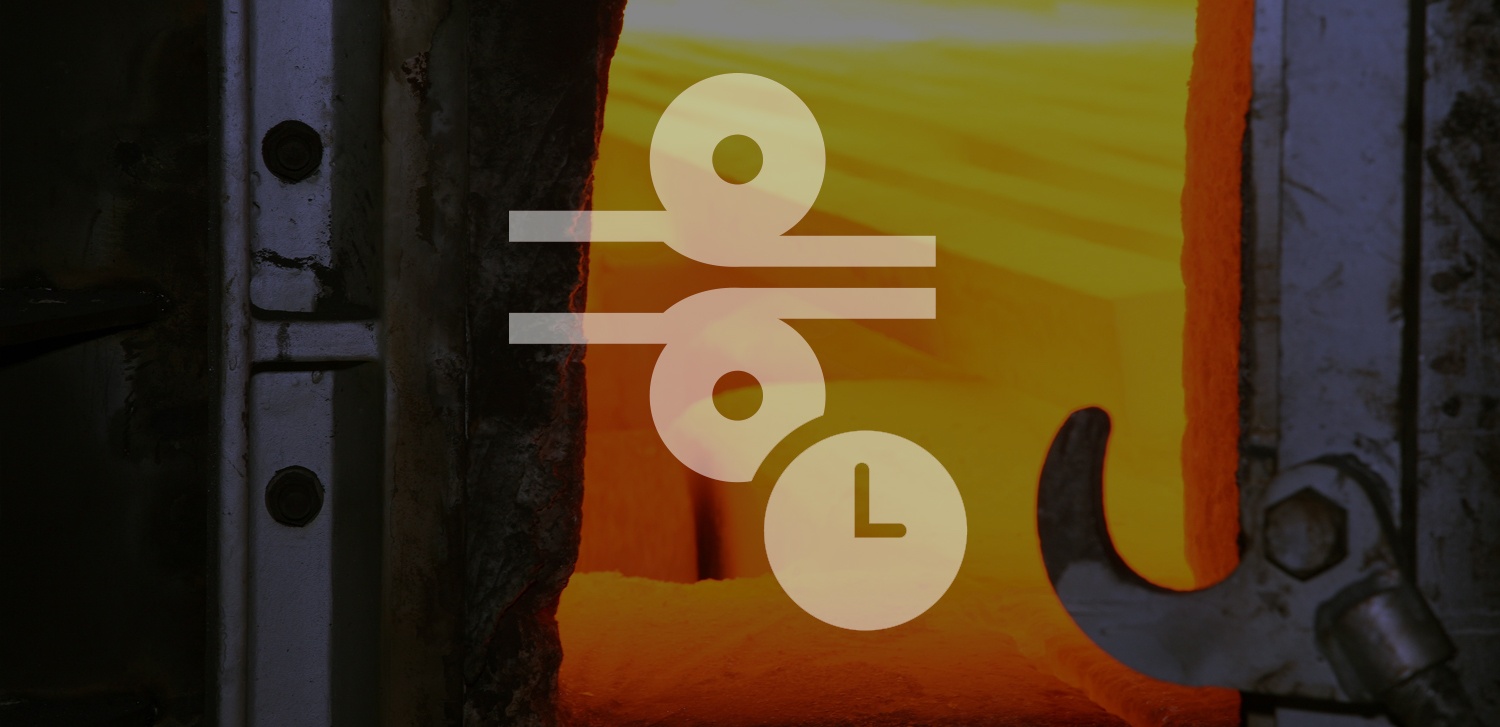
Alarms & Events
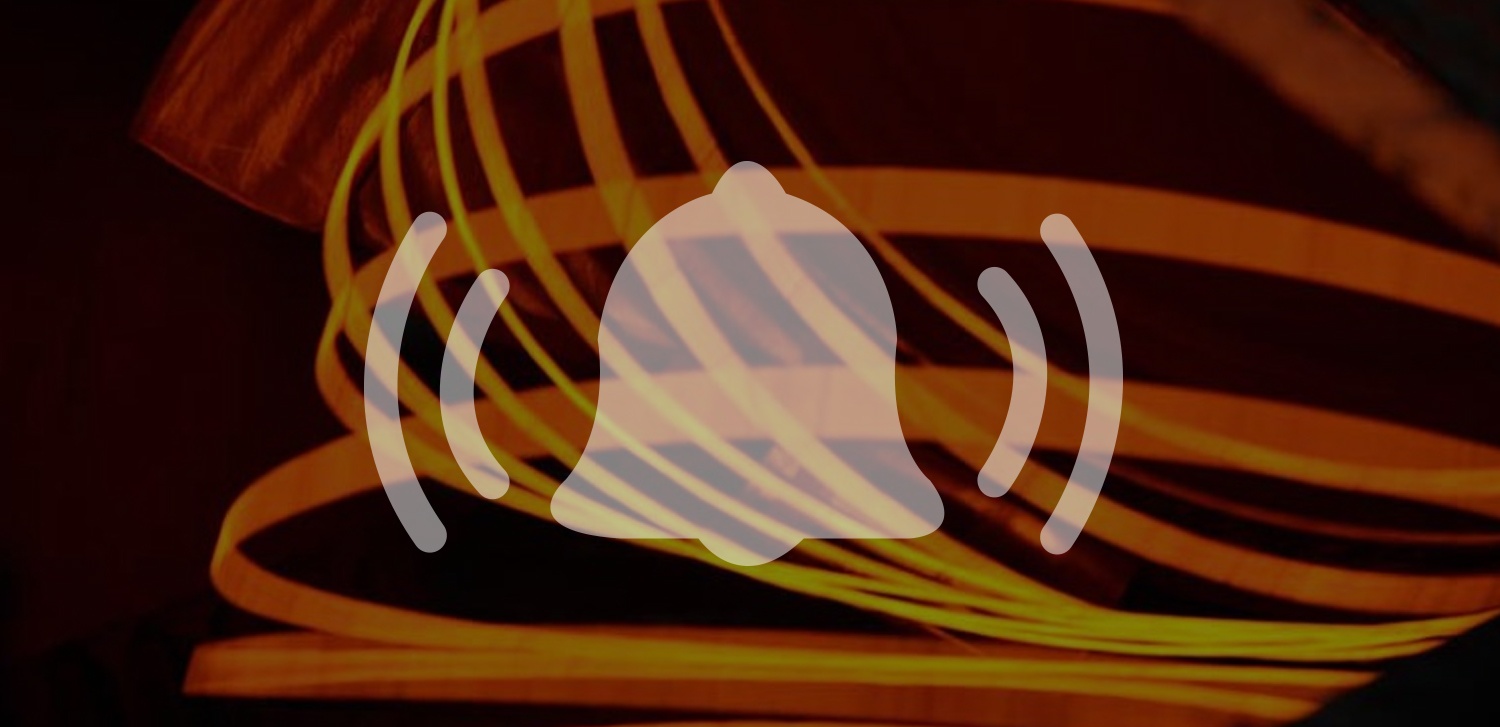
Roll Shop
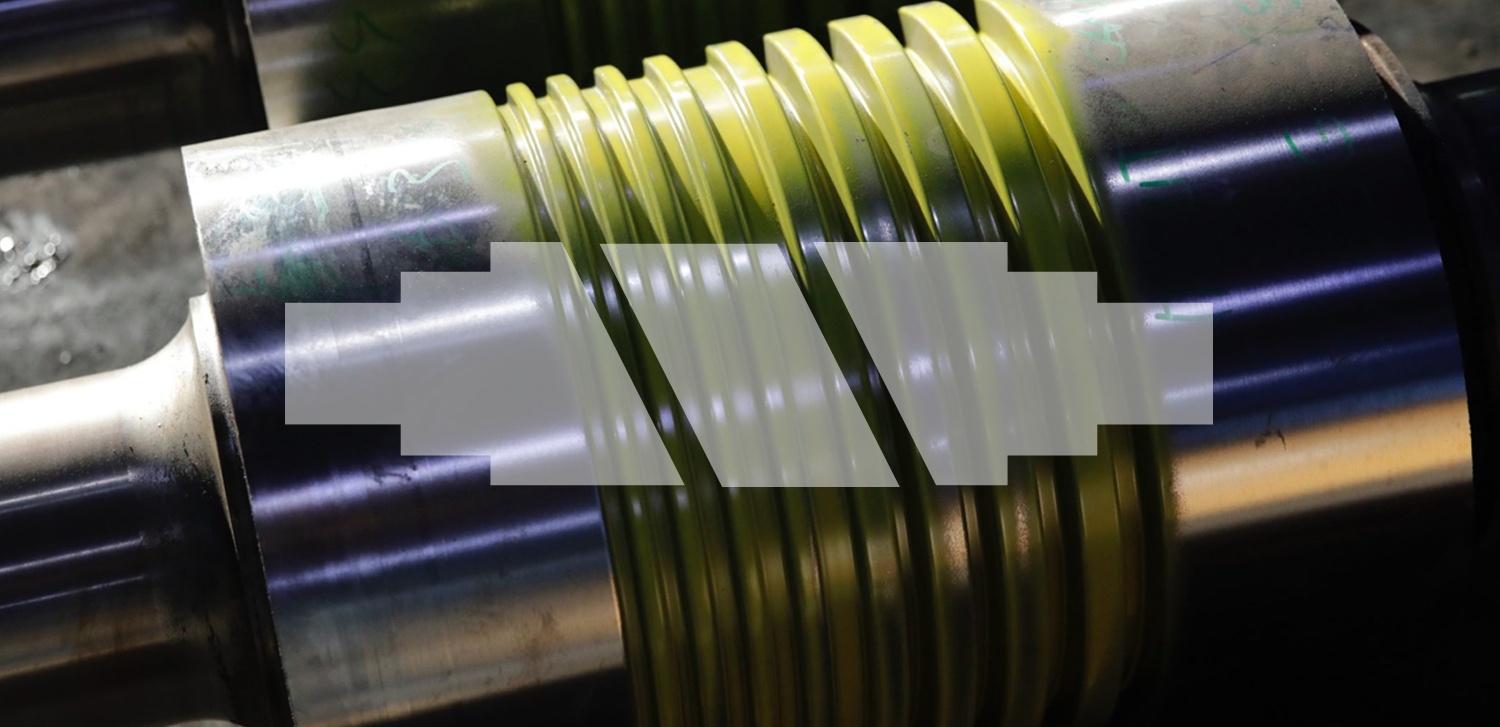
Mill setup
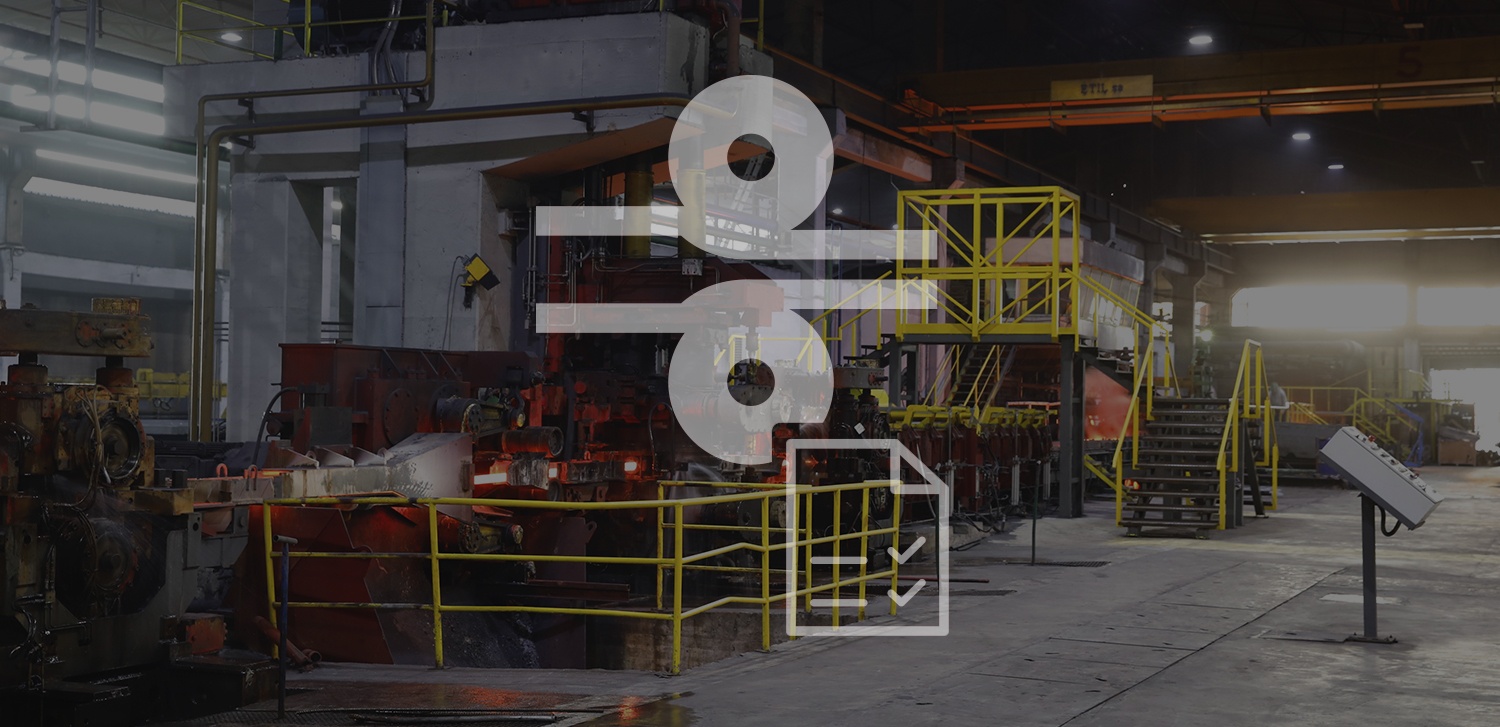
- Current rolling mill layout setup,
- Available equipment,
- Available rolls,
- Cost and setup time information.
Recipes
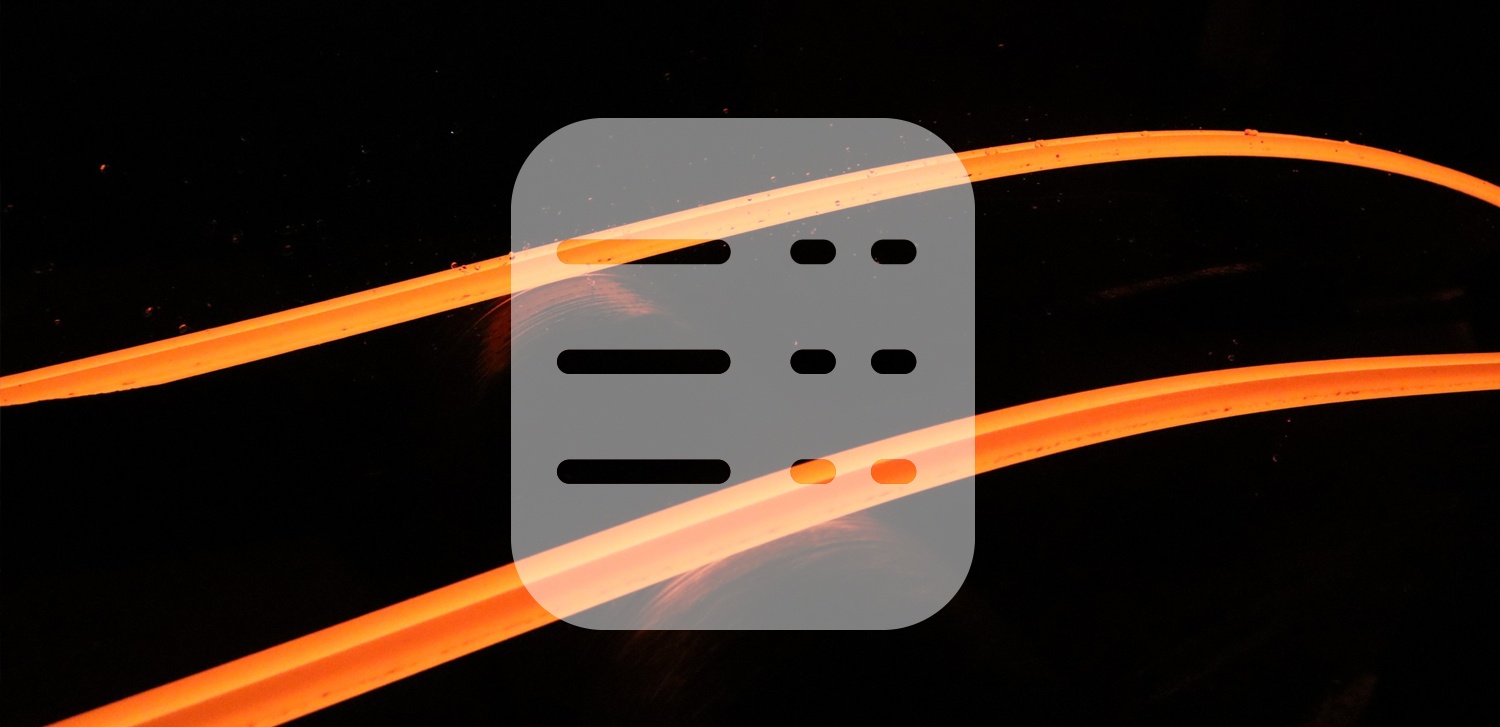
Combining efficiency and accuracy
Roll Shop and Mill Setup Benefits
- Preview future production scenarios
- Visibility of available equipment for scheduled production
- Fast and effective decision making with cost and setup-time analysis
- Preventive maintenance is simple and easy
- Taking decisions based on reliable real time data from rolling mill
- Full native integration with Mill Pulse®
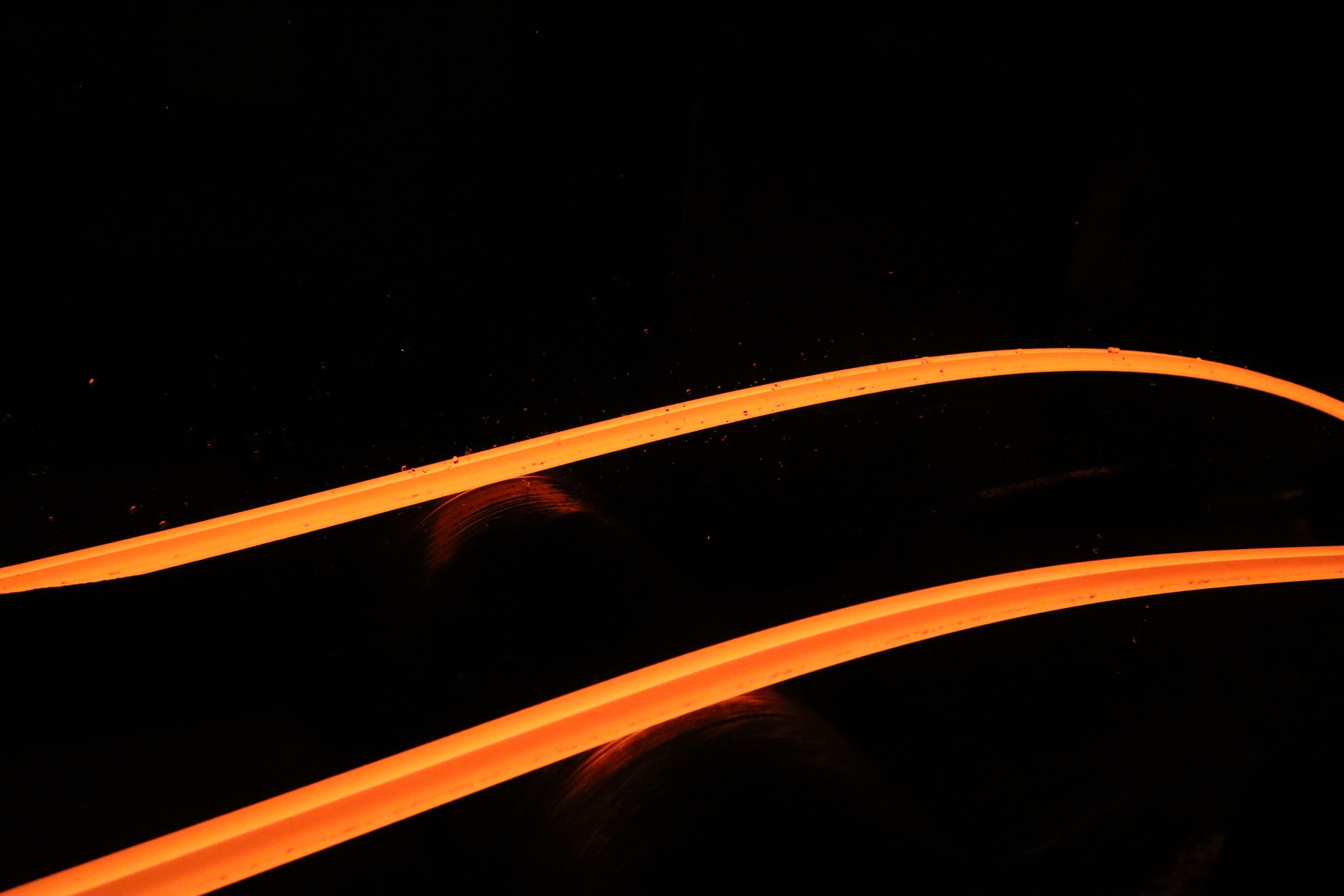
- Fast and effective decision making with cost and setup-time analysis, previewing future production scenarios through a user-friendly comparison tool.
- Online addition of workshop information shows availability and status of the assembled stands, rolls, guides, and consumable parts.
- User can rapidly access a status list for all the roll shop activities and available equipment for the scheduled production requirements.
- Preventive maintenance is simplified by making decisions based on the real rolling tons and equipment issues. Maintenance activities can also be previewed through Mill Pulse® warnings and notices about equipment wear life.
- All information related to change in layout of the rolling mill stands is registered in Mill Pulse® database, so the Historic and Traceability data is built from various dimensions, being able to be contextualized to Production Orders, Events, Delays, and other relevant info about production.
- Roll Shop and Mill Setup are fully integrated with Mill Pulse® and are also open to integrate with other systems.
- Human errors are minimized in the Setup process due to e-checks and work orders that are generated automatically. The setup process is supervised and controlled though Mill Pulse®, which minimize human mistakes when preconditions are forgotten to be checked.
- Checklists are fast and easy to complete for the user, some of them are automatically checked within the automation system.
- Mill Pulse® integrates data collection from the automation system (working hours, rolled tons, etc.) and manual data inputted by the operations in the form of checklists, notes and observations. Altogether the data makes up the Mill Setup workflow process, giving supervisor a global panorama of the setup time and enhancing future analysis.
RUSSULA'S
Roll Shop Management
Management of workshop activities, machining historical records for rolls and grooves. and also those related with consumables such as pinch rolls guides, water cooling nozzles, equalization troughs, turn down guides and laying head pipes. Useful life is automatically registered and updated by the rolling process.
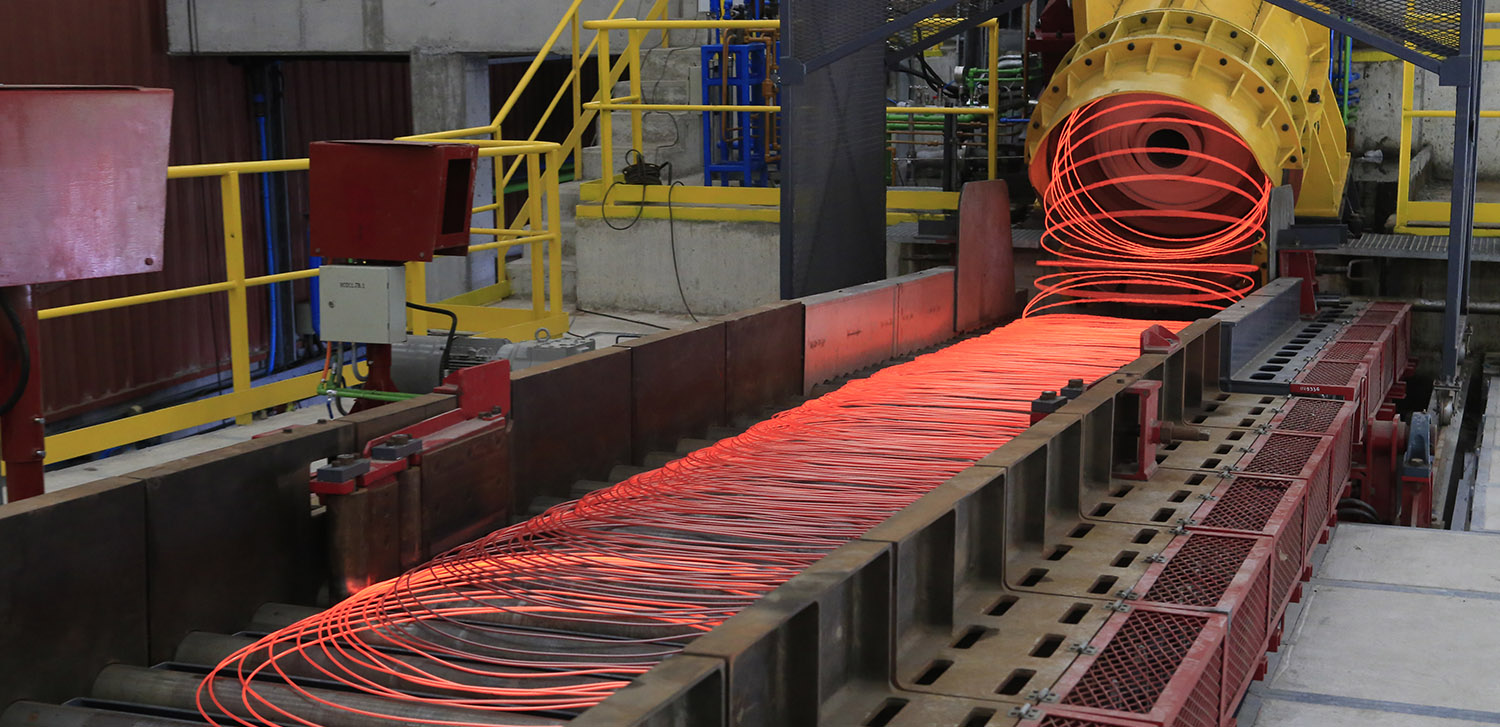
- Management of workshop activities and the consumables parts used by the rolling process.
- Coordinates internal workshop activities and also for external suppliers.
- Definition, querying and management of the existing stock of rolls, guides and consumable parts.
- Automatic tracking of rolled tons per equipment.
- Historical data of the rolls, guides and consumables parts.
- Log of products and setups
- Scheduled assembly plan for rolls and consumables.
- Rolls and grooves machining historical records.
- Tracking capability to record rolls lifetime when there are multiple grooves for slitting.
- Automated collection of data from the PLCs (working hours, rolled tons, etc.)
- Tracking of consumables parts as pinch rolls guides, water cooling nozzles, equalization throughs, turn down guides and laying head pipes
- Native integration with the other Mill Pulse® modules.
RUSSULA'S
Mill Setup
Mill Setup harmonizes and facilitates all tasks related to the current mill equipment setup, empowering the plant to make decisions when equipment changes are required by coordinating and integrating the necessary activities for the rolling mill and workshop.
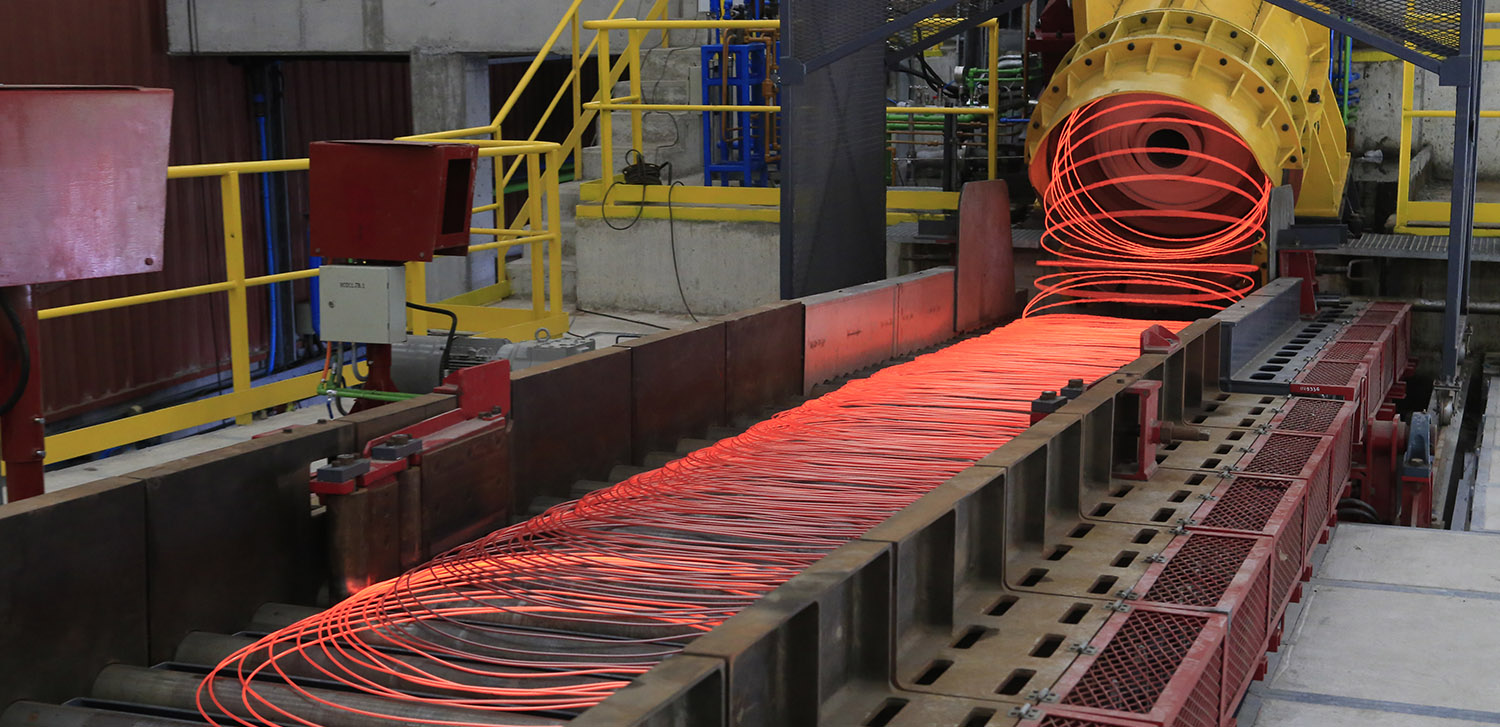
- Mill Setup enables and facilitates all tasks related to the mill equipment setup, linking rolling process and workshop.
- Mill Setup could be requested due to production schedule (business priorities), due to incidentals or due to wear.
- Mill Setup consider management of Work Orders for activities on the roll shop in order to execute a Mill Setup.
- A detailed Checklist is automatically generated with all the activities on the product change.
- Check list helps production staff to verify activities to do, simplifying and minimizing errors during product changes.
- Optimization of the decisions based on availability, setup time and costs.
Finish first with Mill Pulse®
Please fill out the form below to download the Mill Pulse® brochure.